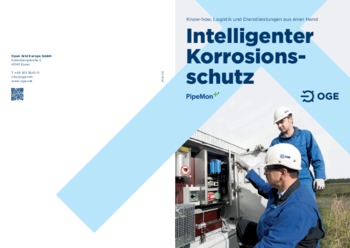
Safety
Effective corrosion protection: Keep your pipes rust-free.
Corrosion protection is extremely important for natural gas pipelines to ensure the commercial viability and longevity of the system. Make use of the corrosion protection services from the German leader in this field of competence.
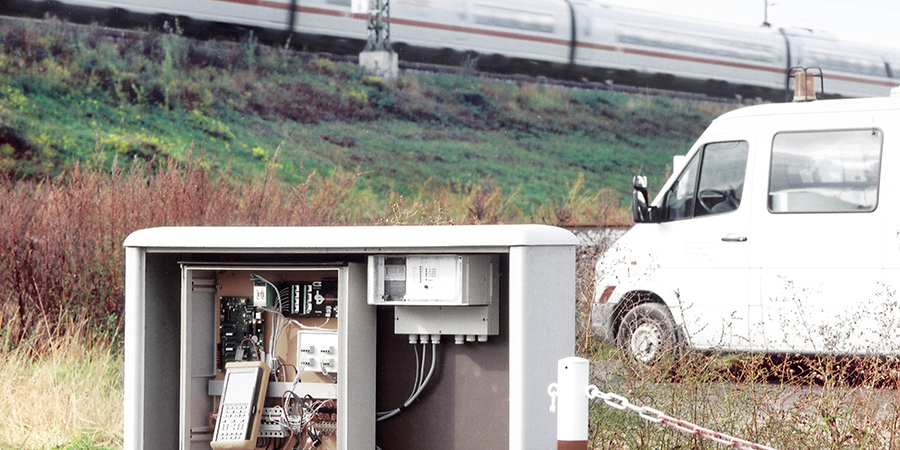
Our specialists develop new components and undertake research to provide forward-looking corrosion protection. We design, build and monitor corrosion protection systems for pipelines, compressor and pumping stations as well as industrial installations, and provide advice, expert opinions and studies. We can calculate the degree of high-voltage interference on pipelines and build protection systems to prevent hazards for individuals as well as AC corrosion. Further information with a full description of our services is provided in our brochure entitled “Intelligent Corrosion Protection”.
Our services in corrosion protection:
- Passive corrosion protection
- High-voltage interference & AC corrosion
- Accredited expert and specialist services
- Condition assessment
- Training
Cathodic protection (CP)
Cathodic protection actively protects buried steel pipelines from corrosion, thereby extending the service life of your assets. With proper setup and regular checks, the CP system prevents corrosion-related damage.
- Basic and lab-based research
- Design of standard and complex CP systems
- Construction, commissioning and maintenance of CP systems
- (Remote) CP system monitoring in accordance with applicable codes and standards (DGUV, DVGW; TFRL etc.)
- Advice on design and construction of CP systems and components
- Damage assessment
Local cathodic protection (LCP)
Cathodic protection of complex structures, or local cathodic protection (LCP), actively protects buried station piping, supply and control cabling on large compressor stations and M&R stations against corrosion. Our experienced, well-trained personnel are at your disposal for these complex projects.
- Design of new systems and extension of existing systems
- Construction, commissioning and maintenance of LCP systems
- (Remote) LCP system monitoring in accordance with applicable technical codes and standards (DGUV, DIN standards etc.)
- Condition assessments of buried installations on existing sites
- Interference tests incl. analysis of the results and definition of actions based on the test results
Passive corrosion protection / quality assurance
Proper coating of pipeline structures helps protect them from corrosion and maintain their value. We meet the most stringent requirements in terms of coating materials as well as the criteria defining the quality of the coating. To achieve an optimum result, it is imperative for the application of the coating to be supervised and inspected by appropriately qualified personnel.
- Testing of coating materials (above/below ground)
- Drafting of specifications for wrap / paint coatings
- Quality assurance in parallel with the construction of pipeline systems
- Provision of coating and Frosio inspectors as part of expediting and construction measures
- Coating inspector (CI) training programmes
Stray current interference
Stray current interference by third-party structures (CP systems, trams, reinforced concrete foundations, etc.) increases the corrosion risk. We know these challenges from decades of experience and will help you optimise the necessary measures for corrosion protection.
- Measurement-based analysis of the interference situation taking account of the mode of operation of the structure causing the interference
- Assessment of the corrosion risk on the basis of the current regulations and taking into account our findings from the status analysis and integrity investigations
- Selection of the necessary protective and monitoring measures against stray current corrosion
High-voltage interference & AC corrosion
Where new energy transmission systems such as pipeline networks are planned, the legislator wants this infrastructure to be installed in joint "energy corridors". High-voltage power lines running parallel to pipelines result in ohmic and/or inductive high-voltage interference with the pipelines. In addition, AC corrosion can occur in pipelines exposed to high-voltage interference. We analyse and calculate the interference situation and produce bespoke concepts to protect people and equipment. We also develop plans to help you reduce your AC corrosion risks.
- Consultation and training on high-voltage interference
- Calculation of the inductive high-voltage interference of high-voltage overhead power lines and power supply lines for electric traction systems (more than 30 years’ experience in this field)
- Sets of measures to ensure shock protection and reduce the risk of AC corrosion
Accredited expert and specialist services
As a "corrosion protection pioneer", OGE is a specialist company certified to DVGW Code of Practice GW 11 which can support you in resolving your problems. The team includes experts accredited to DVGW Code of Practice GW 101, experts according to DIN EN 15257 Level 3 and Frosio-certified coating specialists.
Using this expertise, we conduct surveys and status analyses or damage inspections on your structures and pipelines. On the basis of these we then elaborate optimisation solutions to preserve the value and integrity of your assets.
- Damage analyses, status surveys and expert appraisals
- Expert opinions in accordance with GW101
- Reports and investigations by Frosio experts
Condition assessment
High-pressure gas pipelines built in past years and decades were designed, constructed and commissioned in accordance with the then state of the art. During their years of operation, they underwent regular maintenance and repairs. In terms of corrosion protection this often meant that "integral" information about CP effectiveness is available from measurement data collected as part of CP system monitoring. However, these measurements generally do not provide any indicators about any local impairment to corrosion protection. This is where it is useful to analyse the system status to obtain a comprehensive assessment of the corrosion protection system. In a further step we also look at the material parameters of the pipeline and its mode of operation (operating pressure etc.). All this information can be combined to provide an integrity statement. OGE offers status analyses for the corrosion protection of the following categories of pipeline:
- For piggable pipelines, intelligent pigging can be carried out to provide exhaustive information about the wall thickness of the pipeline along the entire route. If there are any coating defects, the data allow the local corrosion rate to be estimated and therefore provide information about CP effectiveness and/or targeted measures to improve it.
- For non-piggable pipelines, CP measurement techniques (monitoring measurements, close interval surveys, sleeve pipe measurements) can be used for a status analysis.
- The status of the corrosion protection of piping systems at stations (equipped with cathodic protection systems for complex structures) can be assessed using the CP data and – for limited pipeline lengths – using ultrasound measurements.
Training
On the basis of our extensive operating experience, knowhow from R&D projects and detailed knowledge of the latest codes and standards, we provide basic and advanced-level training on "Corrosion Protection of Buried Structures". These training sessions can be tailored to focus on the specific requirements of DIN EN 15257.
- Fundamentals of corrosion and cathodic protection
- Coatings for buried and above-ground structures/pipelines and quality assurance measures
- Cathodic protection of complex structures
- Installation and monitoring of cathodic protection systems
- CP measuring technology
- Stray current interference due to DC-powered systems
- AC interference due to high-voltage systems (shock hazard protection and AC corrosion)
Are you interested in our products and services?
What is corrosion?
The term “corrosion” describes an electrochemical process that results in a reaction of a metal with its environment and hence in a change of its properties. In everyday language one would say "the steel is rusting". The expert would say that the steel is thermodynamically unstable, certain oxidising agents like oxygen and acids, or a polarisation with anodic currents, cause the iron atoms contained in the metal matrix to migrate to the surrounding electrolyte solution (soil). This process continues for as long as there is a supply of oxidising agents.
What effect does cathodic protection (CP) have?
Experience has shown that the steel surface of a buried structure without cathodic protection corrodes at a rate of 0.1 to 0.2 mm/a in those areas where the coating is damaged. Using cathodic protection, the corrosion rate can generally be reduced to less than 0.01 mm/a (= 1 mm in 100 years). If there is a risk of corrosion due to alternating currents, cathodic protection can reduce the corrosion rate to less than 0.03 mm/a.
How does cathodic protection (CP) work?
The structure to be protected, e.g. a buried pipeline, is connected to the negative terminal of a DC source and thus becomes the cathode in a DC circuit. The positive terminal of the DC source is connected to an anode buried in the ground and via which a DC current (protective current) flows to the “holidays” (= coating holidays = defects) where the steel surface comes into contact with the soil. This triggers various electrochemical processes at the pipe-to-soil interface which interact depending on the specific environmental conditions to reduce the corrosion rate:
- The potential of the steel surface is made more negative
- The oxygen at the steel surface is reduced (=“consumed”)
- The pH of the steel surface increases
What kinds of structures are suitable for cathodic protection?
Steel structures (e.g. pipelines) can be equipped with cathodic protection (CP) systems, if their surface is in contact with an electrolyte solution (soil etc.) via which a cathodic current can be delivered to the structure. As well as buried or offshore pipelines, the interior surfaces of water tanks or the reinforcing elements of reinforced concrete structures can also be protected against corrosion using cathodic methods. For cost and electrical engineering reasons it is often practical to provide the surfaces to be protected with a firmly adhering coating made of insulating plastics. The effect of the cathodic corrosion protection can then be restricted to the smaller defects occurring randomly during pipeline operation.
What does potential mean?
This term is a rather imprecise way of describing the measured value for the voltage between a reference electrode and a structure (e.g. a buried pipeline). As the potential of the reference electrode remains constant under all circumstances, the above mentioned measured value is simply designated “potential”, whereby the type of reference electrode against which the measured value has been determined must be specified (generally a saturated Cu/CuSO4 electrode is used with a voltage of 320 mV against the standard hydrogen electrode). The potential of the structure that has been determined in this way is initially “only” a kind of mean value of the electrochemical conditions of all pipe coating defects. By using a suitable measuring technique (so-called "intensive measurements", similar to a “close interval survey”) the potential of a single coating defect can often be determined with a good degree of accuracy. As the potential is a parameter for the electrochemical conditions at the steel/soil phase boundary, the measured value provides information about the corrosion protection or a possible corrosion risk at this location.
What is passive corrosion protection?
This term covers all corrosion protection measures used to isolate steel surfaces to be protected from the surrounding (corrosive) medium. Typical passive corrosion measures include the coating of pipes with 3-ply polyethylene systems for below-ground applications or corrosion protection coatings for pipes and fittings above ground. Generally, a distinction is made between coatings applied by the pipa manufacturer (factory coatings) and those applied on site (field-applied coatings). Local damage to a factory or field-applied coating that exposes the steel surface underneath is often referred to as a “holiday”.
What are stray current interference and stray current corrosion?
Stray current interference results from all structures that cause DC currents to flow in the ground. These include, for example, cathodically protected pipelines and their anodes, DC-powered trams, but also reinforced concrete foundations. The DC currents cause local changes to the potential of the soil, as a result of which the potential of a third-party structure/system in this area is influenced, i.e. changed. Generally, a positive change in potential leads to an increase in the corrosion rate (stray current corrosion), while a negative change of potential reduces the corrosion rate.
What does high-voltage interference mean?
High-voltage interference occurs when an AC voltage is induced on an intersecting or parallel pipeline due to the operation of an AC system (three-phase AC high-voltage line, transformer substation, electrified rail line etc., frequency 50 Hz or 16 2/3 Hz). In this context, a distinction is made between interference mechanisms: ohmic (due to currents in the ground), inductive (due to the magnetic field of the AC currents) and capacitive (due to the electrical field of the high-voltage system). The magnitude of the AC voltage induced in a pipeline has to be limited to 60 V to protect against electric shock. Voltages of up to 1000 V are only permissible for short-term faults (< 0.2 s) on the high-voltage systems. Induced AC voltages are also the cause of AC corrosion.
High-voltage direct current transmission (HVDC) systems can also affect buried piping. Direct currents induced in the pipeline via the soil can also lead to stray current corrosion; switching processes in HVDC lines and systems cause a short-term inductive effect.
What is AC corrosion?
This term describes a corrosion mechanism whereby, in addition to a protective current (from the CP system), an alternating current (due to high-voltage interference) many times higher than the protective current also flows into a coating defect via the steel/soil phase boundary. The current densities, i.e. the protective and AC currents referred to the surface of the defect, are decisive for evaluating the risk of AC corrosion. Under unfavourable conditions, an increased corrosion rate will result due to the repeated build-up and subsequent destruction of a passive layer (oxide layer) at molecular level during every anodic cycle of alternating current. Sufficient protection against AC corrosion can be achieved through targeted control of protective and alternating current densities.
Why is it sensible to install cathodic corrosion protection?
Provided that the necessary conditions (longitudinal conductivity, electrical isolation from earthed structures, good coating, contact with ground all round) are observed when building a structure like a buried pipeline, cathodic protection is a cost-effective way of preserving the value of your investment. The relevant regulations prescribe the use of CP for high-pressure gas pipelines and pipelines carrying media hazardous to water, making CP both an operational safety and an environmental protection measure.
Downloads
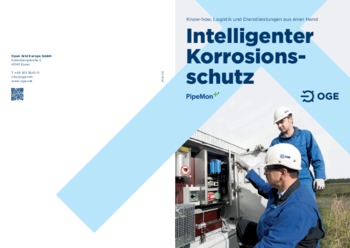
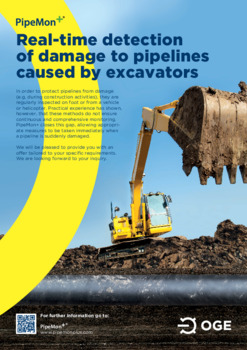
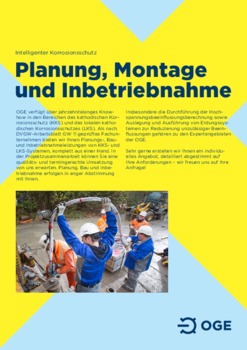
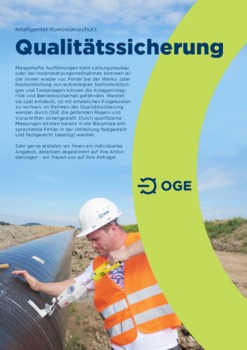
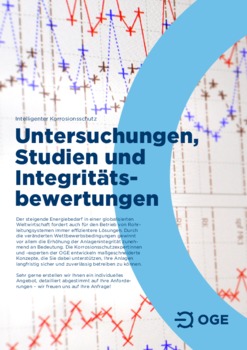